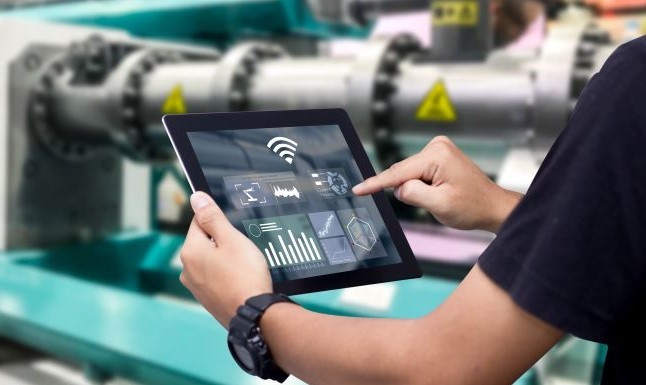
O monitoramento abrangente dos equipamentos rotativos pode ser benéfico para as equipes de manutenção de muitas maneiras, principalmente pela “observação” de equipamentos para possíveis problemas dia e noite. Hoje em dia, muitas equipes se surpreendem com as economias oferecidas por essa nova tecnologia.
Quando o sensor rastreia todos os fatores envolvidos no monitoramento do equipamento (temperatura da superfície, aceleração ou velocidade de vibração, pressão do processo e temperatura do processo), os usuários podem facilmente identificar problemas potenciais precocemente e corrigi-los antes de falhas às vezes catastróficas e caras do selo, bomba/misturador ou agitador e outros componentes.
O rastreamento dessas condições também pode ajudar as equipes a identificar a causa raiz de falhas que não são resolvidas por uma inspeção presencial. Apenas mensalmente, essas novas capacidades podem economizar dezenas de milhares de dólares em um único andar.
Por essa razão, muitas equipes de manutenção estão adotando tecnologia inovadora, como o monitoramento rotativo de equipamentos, para transformar seus “equipamentos preventivos” em “equipamentos de confiabilidade”.
Práticas típicas de manutenção
As práticas de manutenção de equipamentos no setor de processos e serviços são essencialmente divididas em três tipos diferentes:
- Reativo: Quando a manutenção é reativa, o equipamento é operado até falhar. Em uma abordagem reativa, há custos ocultos, como aumento do tempo de inatividade da fábrica, interrupções na entrega aos clientes, perda de tempo à espera de ferramentas e mão-de-obra, altos custos de horas extras, estoques elevados ou estoques muitas vezes esgotados.
- Preventivo: Quando a manutenção é preventiva, o equipamento é verificado/reparado em horários pré-determinados. Para estabelecer programas de manutenção preventiva, é necessária uma estimativa conservadora da vida útil esperada do equipamento. Infelizmente, essas estimativas podem ser caras porque os componentes substituídos podem ter funcionado por um período maior. Os problemas podem passar despercebidos e levar a falhas e, às vezes, paradas não planejadas.
- Preditivo: Quando a manutenção é preditiva, é possível identificar quando e por que um componente falhará. Em uma abordagem preditiva: peças de reposição são encomendadas bem a tempo; as paralisações são planejadas e somente quando necessário; e as taxas de falha e danos aos equipamentos são menores, resultando em maior segurança e confiabilidade do equipamento.
Método Antigo
Para equipamentos rotativos, a manutenção reativa e preventiva tem sido historicamente a norma. O método mais comum utilizado é monitorar a vibração e a temperatura da superfície. Essas medidas são frequentemente realizadas por um técnico treinado em vibração que faz medições em um determinado momento e segue um cronograma fixo.
O técnico percorre a planta coletando medidas para identificar a assinatura específica da vibração e fornecer recomendações de manutenção. No entanto, os piores eventos de vibração nem sempre correspondem à agenda do técnico. Portanto, com este método de monitoramento de vibração, o técnico não pode observar eventos de vibração prejudiciais que ocorrem no computador durante horas ociosas.
Método atual
Com sensores de monitoramento inteligentes, a facilidade de coleta, visualização e interpretação de dados é importante para identificar rapidamente mudanças nos equipamentos.
O uso de sensores de monitoramento inteligentes ajuda a tornar a manutenção preditiva onde ajustes adequados do equipamento podem ser feitos conforme necessário e quando necessário. Investir nas ferramentas certas pode simplificar e melhorar muito a manutenção da bomba.
Novos conhecimentos de manutenção com o sensor Chesterton Connect ™
Com mais de 135 anos de experiência em bombas e vedações, a A.W. Chesterton Company desenvolveu recentemente um sensor de monitoramento inteligente para equipamentos rotativos para detectar fatores que afetam vedações e rolamentos e facilitar a manutenção preditiva dos equipamentos. Este produto agora é usado em todo o mundo para ajudar as equipes de manutenção a alcançar um novo nível de confiabilidade e redução de custos.
Chesterton Connect é um sensor de monitoramento inteligente sem fio 24 horas por dia, 7 horas por dia, 700 anos, que detecta variações em:
- Pressão e temperatura do processo: causada por restrições à sucção, descarga, câmara de vedação, plano ambiental de vedação dupla, velocidade do eixo, etc. para determinar o que está acontecendo dentro do selo/bomba e para evitar (ou encontrar) a causa raiz da falha do selo.
- Vibração e temperatura da superfície: causada por cavitação, desalinhamento do equipamento, desequilíbrio do impulsor e outros problemas, para determinar quando é o melhor momento para o técnico avaliar o sinal de vibração do equipamento.
O sensor Chesterton Connect fornece monitoramento completo e fácil de usar de todos os equipamentos rotativos para aumentar a confiabilidade, segurança e desempenho dos equipamentos. A instalação leva menos de dois minutos. A coleta de dados 24 horas por dia, 7 horas por dia, 7% é fácil e o aplicativo móvel fácil de usar permite visualização e interpretação de dados fáceis e seguros.
A seguir, os casos em que o sensor Chesterton Connect foi usado e economias imediatas foram obtidas no equipamento:
Estudo de Caso nº 1: Identificando condições de descarga de vedação
Uma usina de gerenciamento de resíduos estava operando uma bomba centrífuga pesada para processar os lodos. Apesar da instalação de uma vedação mecânica robusta, a confiabilidade da bomba não foi satisfatória e o selo continuou a falhar. Algo claramente não estava certo com a operação, mas ninguém tinha uma resposta.
O representante local de Chesterton recomendou um selo mecânico Chesterton 155 ainda mais protegido por uma bucha ativa da garganta SpiralTrac ™.
Um sensor Chesterton Connect™ foi instalado para monitorar parâmetros de processo na câmara de vedação e entender as causas de repetidas falhas de vedação.
O Chesterton Connect foi configurado para monitorar o selo 24 horas por dia, 7 horas por dia, 7 horas por semana e revelou que, durante o turno da noite, ao interagir com as
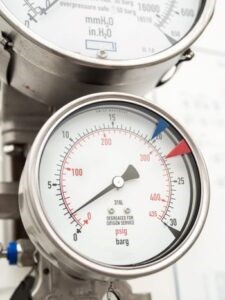
bombas, o operador muitas vezes esqueceu de ativar a água de descarga/água da barreira. Com base nesses achados, os funcionários puderam fazer correções no cronograma de trabalho, aumentando a confiabilidade geral. A bomba está funcionando corretamente e sem falhas.
Estudo de Caso nº 2: Problemas de vibração da bomba
Em uma planta de papel, uma bomba de lodo hidratante crítica com alta concentração de sólidos apresentava vibrações altas e pouco frequentes que representavam uma ameaça à confiabilidade do equipamento. O especialista em vibração só foi capaz de fazer medições pontuais e não pôde detectar quando a vibração atingiu o pico.
O sensor Chesterton Connect foi instalado em um selo mecânico Chesterton 180 para monitorar a pressão e a temperatura no paraquedas, bem como no rolamento radial externo para monitorar a vibração e a temperatura da superfície.
Com o sensor Chesterton Connect, o usuário foi capaz de monitorar a vibração 24 horas por dia, 7 dias por semana, acessar dados históricos e entender com precisão quando a alta vibração estava ocorrendo.
Graças aos alertas em tempo real do sensor Chesterton Connect, o especialista em vibração foi chamado quando a vibração estava no seu auge e o cliente foi capaz de detectar o problema causando a alta vibração.
O cliente foi capaz de aplicar com sucesso avaliações de manutenção adequadas para evitar que vibrações altas e pouco frequentes danifiquem equipamentos críticos.