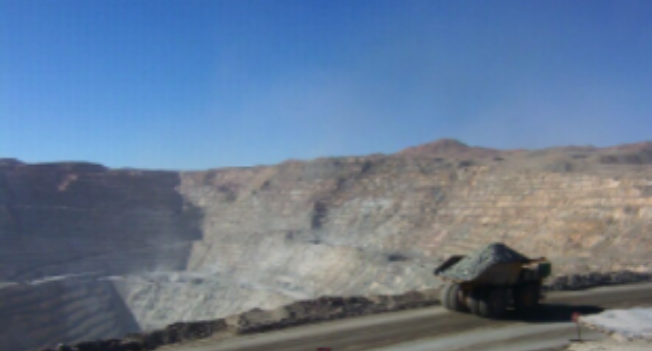
Sabe-se que todas as atividades de mineração têm um problema comum que não só afeta o funcionamento da planta, mas, o mais importante, o resultado final. Este problema se chama ABRASÃO.
Nos últimos 30-35 anos, tecnologias de revestimento reforçado de cerâmica foram introduzidas no mercado e a indústria de mineração não ficou muito atrás como potenciais usuários. No artigo seguinte vamos analisar quais são exatamente os benefícios e quais as vantagens que apresentam em relação às tecnologias tradicionais de proteção à abrasão e até mesmo às mais novas técnicas e materiais.
A partir do momento em que o minério começa a ser transferido por algum método para a fábrica de processamento, para onde o produto final é manuseado encontraremos equipamentos que sofrem abrasão. Podemos até encontrar equipamentos que podem durar até uma semana, devido às condições abrasivas do meio ambiente.
Antes de analisarmos como proteger os equipamentos do desgaste, é necessário classificar os modos de abrasão, que resultam em superfícies de equipamento sendo afetadas e desgastadas:
Abrasão de três corpos: Eles correspondem a duas superfícies duras e algum tipo de partículas entre elas. Isso é caracterizado por uma ou ambas as superfícies duras em movimento e há uma força aplicada por elas às partículas, resultando em uma redução do tamanho das partículas e uma consequente abrasão dos corpos duros.
Abrasão de dois corpos: Neste tipo de abrasão, geralmente há uma superfície dura estática e partículas que deslizam paralelamente a ela. Esse processo afeta a superfície e sua espessura.
Abrasão impacto/impacto: Esse tipo de abrasão é observado quando um fluxo de partículas não desliza paralelamente a uma superfície dura, mas em um ângulo e, portanto, as partículas estão impactando a superfície formando “marcas profundas” devido a um efeito ranhurado produzido pelas partículas na superfície.
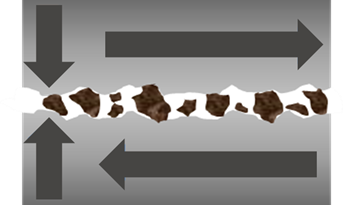
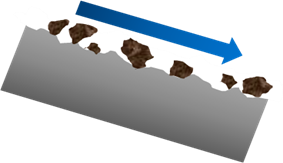
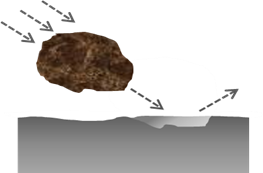
A agressividade e a gravidade de um processo de abrasão nas últimas situações descritas são influenciadas pelos seguintes fatores:
- Dureza de partículas: Quanto mais dura a partícula, maior o processo de abrasão.
- A forma das partículas: Formas irregulares resultam em abrasão mais agressiva.
- A densidade das partículas: Afeta especialmente o impacto, quanto maior a densidade, mais penetrará em uma superfície.
- Tamanho e peso de partículas: Partículas maiores/mais pesadas gerarão mais abrasão.
- Velocidade de partículas: Em velocidades mais altas, o processo de abrasão aumenta.
- Diferença na dureza entre partículas e superfícies duras: Partículas mais duras produzem mais abrasão.
- Força de impacto: Geralmente relacionados com a altura das partículas caindo em uma superfície dura
- Mistura de partículas molhadas ou secas: Onde a mistura seca é mais agressiva do que uma mistura molhada.
- Porcentagem de partículas sólidas no armazenamento: Quanto maior o percentual, mais abrasivo será o processo.
- Fluxo de massa: A uma taxa de fluxo mais alta, o nível de abrasão aumenta.
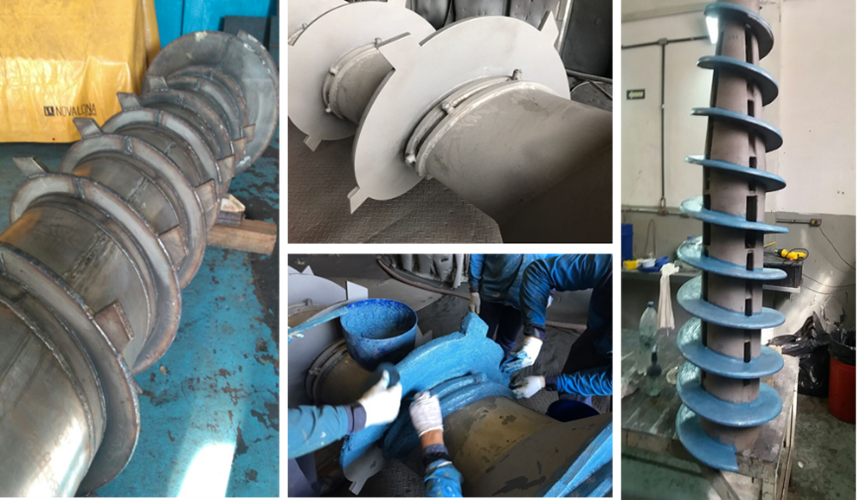
Alternativas tradicionais de proteção contra a abrasão
Tradicionalmente, nas instalações de mineração e processamento mineral, o principal método utilizado para reduzir os efeitos da abrasão de três corpos é o uso de ligas metálicas de alta dureza. No que se refere à abrasão de dois corpos e impacto, o uso da borracha em suas diferentes formas tem sido utilizado como revestimento/revestimento protetor e sacrificial para equipamentos expostos a situações de abrasão e, em algumas situações, também é utilizado o uso de ligas metálicas duras.
As características desses métodos de proteção são as seguintes:
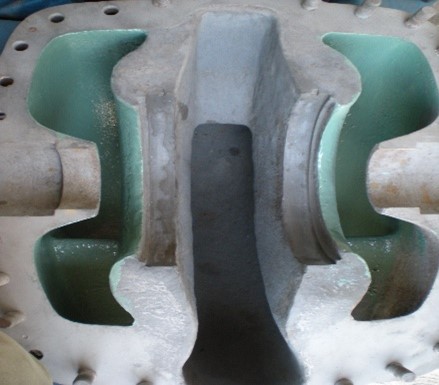
Revestimento de Borracha
Vantagens dos revestimentos de borracha
- Boa proteção contra corrosão
- Eles têm ampla resistência química, dependendo do tipo de borracha.
- Pode ser usado em uma ampla gama de temperaturas
- Tem boa resistência à abrasão
- Tenha excelente resistência ao impacto
- Pode se adaptar a qualquer forma
- Menor peso que revestimentos de aço
Limitações dos revestimentos de borracha
- Partículas deslizantes (especialmente afiadas) podem danificar a superfície
- O limite de temperatura é geralmente em torno de 132°C, mas para uretanos, que estão relacionados à resistência à abrasão, a temperatura máxima é de 70°C.
- Possibilidade de permeação nas costuras, quando aplicada em folhas
- Baixa adesão ao substrato, normalmente inferior a 1.000 psi (70 kg/cm2)
- Alto custo de aplicação, vulcanizado ou em laminados
- Difícil de aplicar no campo, especialmente quando a vulcanização é necessária.
Revestimento de aço endurecido.
Vantagens dos revestimentos de aço endurecido
- Muito boa resistência ao desgaste
- Boa resistência química e de corrosão
- Excelente força compressiva
- Resistência a temperaturas extremamente altas
- Pode ser pré-fabricado de certas maneiras.
- As placas de desgaste podem ser fabricadas em dois tipos de alusões (placas bimetálicas) para reduzir o peso sem comprometer a resistência à abrasão.
Limitações dos revestimentos de aço endurecido
- As alianças mais duras tendem a ser frágeis e romper com o impacto
- Não pode ser reparado quando usado, não pode ser soldado.
- A maioria das ligas de aço inoxidável são muito sensíveis aos cloretos.
- Difícil trocar placas de desgaste devido ao alto peso
- A maioria das aplicações de placas de desgaste estão ferradas, dificultando algumas aplicações.
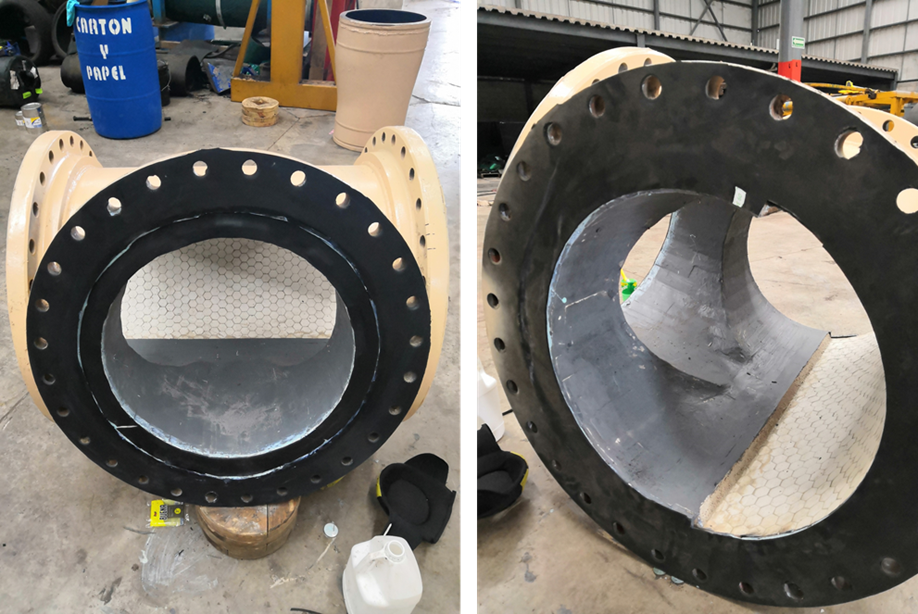
Últimas alternativas de proteção contra abrasão
À medida que os avanços tecnológicos ocorriam e a necessidade da indústria de se proteger contra a abrasão tornou-se cada vez mais crucial devido à flutuação do preço do cobre no mercado, algumas novas alternativas passaram a desempenhar um papel importante nessa área:
- Ladrilhos de cerâmica: Eles têm a vantagem de fornecer uma dureza superficial, perdendo apenas para o diamante. Isso faz dessas telhas uma excelente escolha para resistir à abrasão de dois corpos por deslizamento paralelo.
As principais limitações são baixa resistência ao impacto e baixa adesão à superfície, o que pode resultar em delaminação. Além disso, eles exigem muito tempo de instalação e são muito difíceis de proteger geometrias irregulares ou não quadradas.
- Revestimentos de borracha-cerâmica: Esta opção combina o melhor de duas tecnologias, a extrema resistência à abrasão de telhas cerâmicas e a extrema resistência ao impacto da borracha. Isso faz desta alternativa uma excelente escolha em grandes funis de partículas e caixas de transferência.
A principal limitação está relacionada ao tempo de instalá-los, seja parafusando-os ou colando-os. Eles também são bastante pesados (20-60 libras); portanto, às vezes eles requerem equipamentos especiais para instalar. Eles tendem a usar de forma irregular, como a maioria das superfícies expostas a um ambiente abrasivo, e não têm um método de reparo além de mudar uma placa inteira.
- Revestimentos reforçados cerâmicos: Também aproveitam a dureza da cerâmica ligada por uma resina de polímero, onde não só a superfície é resistente à abrasão, mas também pode se adaptar a qualquer forma e espessuras diferentes.
As limitações estão relacionadas a temperaturas acima de 204°C e situações de impacto extremo. Além disso, eles requerem um tempo mínimo de cura para alcançar a dureza adequada da resina antes que possam ser expostos a uma situação de abrasão.
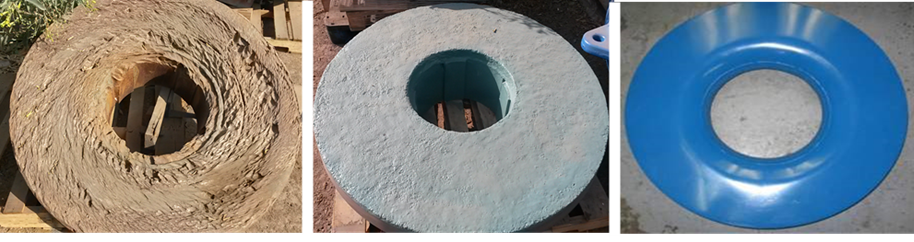
Benefícios e vantagens dos revestimentos reforçados cerâmicos
Nos últimos 30-35 anos, tecnologias de revestimento reforçado de cerâmica foram introduzidas no mercado e a indústria de mineração não ficou muito atrás como potenciais usuários. Por uma questão de fato; a indústria do cobre no Chile vem usando essas tecnologias desde o final da década de 1980 e a cada ano tem visto cada vez mais benefícios de fazê-lo.
Vamos discutir, quais são exatamente os benefícios e quais as vantagens presentes em relação às tecnologias tradicionais de proteção à abrasão e até mesmo às mais novas técnicas e materiais?
- A abrasão é um dos fatores com maior influência da produção nas operações de mineração de cobre. O montante de fundos que são gastos diariamente para reparar/substituir equipamentos gastos é esmagador.
- O tempo de inatividade da produção é outro fator extremamente importante, parar certos equipamentos de produção em grandes minas de cobre, pode significar perdas relacionadas à produção de US $ 50.000 por hora ou até mais.
- Disponibilidade de equipamentos, este ponto se relaciona diretamente com os custos de inatividade onde cada vez que uma equipe requer reparo deve ser interrompida, então a indústria está sempre procurando soluções mais duráveis.
- A facilidade de solução também tem impacto no tempo de inatividade do equipamento, já que quanto mais tempo leva para implementar uma solução resistente à abrasão, maior a perda de produção.
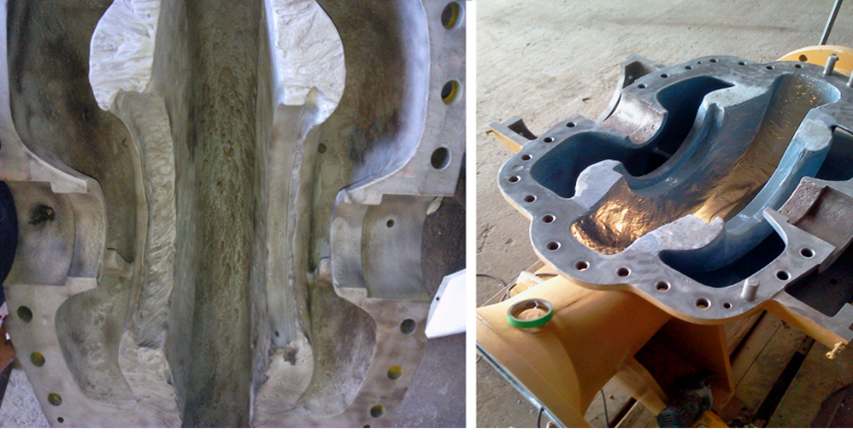
Levando em conta, então, os fatores descritos em último lugar, podemos agora relacioná-los às vantagens que os revestimentos cerâmicos oferecem a esta indústria:
- Eles são a solução mais econômica para suportar condições de abrasão, tanto quanto o custo do revestimento em comparação com o tempo de inatividade do equipamento e a vida útil da solução.
- Fácil de aplicar, portanto, pode ser aplicado na oficina ou no campo, o que também influencia menos perdas de tempo de inatividade.
- Eles podem ser facilmente adaptados a qualquer forma de superfície e geometria do equipamento.
- Eles podem ser usados para reparar equipamentos com tecnologias de proteção contra abrasão de revestimentos novos e tradicionais, economizando tempo em comparação com a remoção de grandes áreas de revestimentos/revestimentos instalados existentes.
- Ele pode ser facilmente reparado, o que significa que o revestimento restante após um período de operação não precisa ser removido, ele só precisa ser limpo para aceitar o novo revestimento em cima.
- Eles podem aderir muito bem a diferentes tipos de superfícies, como metais, borracha, telhas cerâmicas e revestimentos cerâmicos reforçados similares, após a preparação adequada da superfície.
- Eles podem reduzir o inventário de peças de reposição, já que muitas peças agora podem ser reparadas várias vezes, desde que sejam estruturalmente sólidas.
Essas vantagens são porque hoje os revestimentos reforçados cerâmicos são usados na indústria de mineração em todo o mundo para reparar, proteger e revestir equipamentos expostos a condições abrasivas. Existem muitos tipos de revestimentos reforçados cerâmicos, que podem ser resumidos da seguinte forma:
- Quanto ao tamanho do reforço cerâmico:
- Revestimento cerâmico com pincel reforçado com partículas finas, para resistir às condições de abrasão leve.
- Pasta cerâmica reforçada com partículas finas que podem ser aplicadas com espátula, que é usada para encher ou reconstruir, resiste às condições de abrasão leve.
A dureza das partículas de reforço é um fator muito importante para a resistência à abrasão, onde quanto maior a dureza, mais resistente à abrasão. Dito isso, podemos identificar:
- Partes de alto teor alúmina, pureza ≈92%. Eles geralmente são de cor branca e fornecem o maior valor de dureza, mas têm o maior custo.
- Partículas com menor teor de alumina, com pureza de 65 a 75%. Eles geralmente são de cor preta e proporcionam menos dureza do que partículas brancas, mas têm um custo menor.
- Carboneto de tungstênio, essas partículas são tão duras quanto partículas à base de alumina, mas não podem ser formadas em esferas.
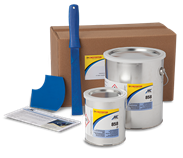
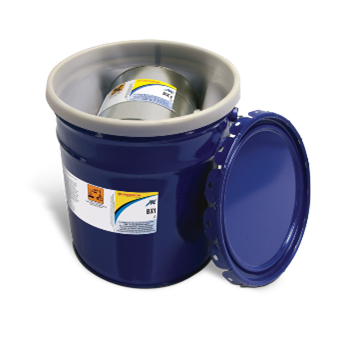
Em conclusão, podemos afirmar com bastante precisão que o uso de revestimentos cerâmicos reforçados em equipamentos sujeitos à abrasão, revolucionou as práticas de manutenção na indústria de processamento de minério de cobre, devido à facilidade de uso, confiabilidade, custo-efetividade e desempenho. Com o desenvolvimento de novas tecnologias, podemos ver que o uso e a necessidade desses tipos de revestimentos só crescerão e a necessidade de desenvolver mais tipos de revestimentos será determinada pelas necessidades do mercado à medida que o tempo avança.
Chesterton protege estruturas críticas e equipamentos com tecnologia avançada de revestimento reforçado ARC há mais de 25 anos. Os materiais compostos ARC são cientificamente projetados para proteger metais e concreto contra os danos e problemas dispendiosos associados à abrasão, erosão, corrosão, ataque químico e corrosão atmosférica.
Se você precisar de ajuda para selecionar um revestimento industrial para um aplicativo específico, entre em contato com nosso serviço de perguntas a um profissional experiente para obter ajuda.
Por Raul Bernales.